Flange Facer Machines: Essential Tools for Precision Machining
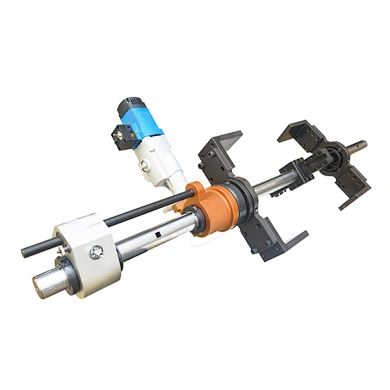
# Flange Facer Machines: Essential Tools for Precision Machining
## Introduction to Flange Facer Machines
Flange facer machines are specialized tools designed for machining and refinishing flange surfaces. These machines play a crucial role in various industries, particularly in pipeline construction, oil and gas, and power generation sectors. Their primary function is to ensure that flange faces meet precise specifications for optimal sealing performance.
## Key Features of Modern Flange Facers
Contemporary flange facer machines incorporate several advanced features that enhance their performance and versatility:
- Portable designs for on-site machining operations
- Precision cutting tools for accurate surface finishing
- Adjustable mounting systems to accommodate various flange sizes
- Robust construction for durability in harsh environments
- Variable speed controls for optimal machining results
## Applications in Industrial Settings
Pipeline Maintenance and Repair
Flange facers are indispensable for maintaining pipeline integrity. They allow technicians to refurbish damaged flange surfaces without requiring complete flange replacement, significantly reducing downtime and costs.
Power Plant Operations
In power generation facilities, these machines ensure proper sealing of high-pressure flanges, preventing leaks and maintaining system efficiency.
Shipbuilding and Marine Applications
The marine industry relies on flange facers to maintain critical piping systems aboard vessels, where space constraints often make portable solutions essential.
## Choosing the Right Flange Facer Machine
When selecting a flange facer machine, consider these important factors:
Factor | Consideration |
---|---|
Flange Size Range | Ensure the machine can handle your typical flange diameters |
Portability | Weight and setup requirements for your work environment |
Power Source | Electric, pneumatic, or hydraulic operation |
Cutting Tool Options | Availability of different tooling for various materials |
Precision Capabilities | Tolerance levels for your specific applications |
## Maintenance and Safety Considerations
Regular Maintenance Practices
To ensure optimal performance and longevity of your flange facer machine:
- Clean and lubricate moving parts regularly
- Inspect cutting tools for wear and replace as needed
- Check alignment and calibration periodically
- Store the machine in a dry, protected environment
Safety Precautions
Always follow these safety guidelines when operating flange facer machines:
- Wear appropriate personal protective equipment (PPE)
- Secure the workpiece properly before machining
- Follow manufacturer’s instructions for setup and operation
- Disconnect power sources when performing maintenance
## Conclusion
Flange facer machines represent a critical investment for industries requiring precision flange machining. Their ability to perform on-site repairs and refinishing operations makes them invaluable tools for maintaining system integrity and reducing operational downtime. By selecting the appropriate machine for your specific needs and following proper maintenance and safety protocols, you can ensure reliable performance and extended service life from your flange facing equipment.