Swiss Screw Machining: Precision and Efficiency in Small Part Manufacturing
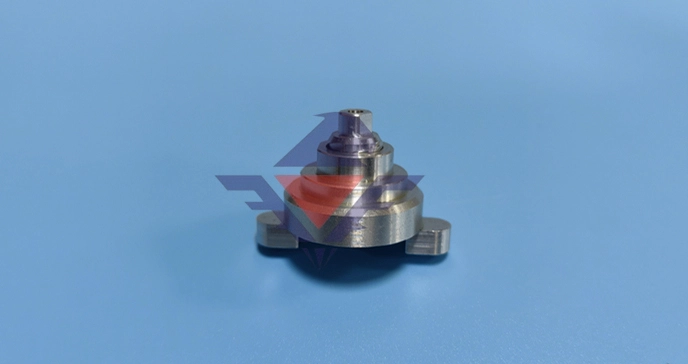
# Swiss Screw Machining: Precision and Efficiency in Small Part Manufacturing
## Introduction to Swiss Screw Machining
Swiss screw machining, also known as Swiss turning or Swiss-style lathe machining, is a specialized manufacturing process that has revolutionized the production of small, complex, and high-precision components. This advanced machining technique originated in Switzerland’s watchmaking industry during the late 19th century and has since become indispensable across various industries requiring tight tolerances and exceptional surface finishes.
## How Swiss Screw Machining Works
The Swiss screw machine operates differently from conventional lathes. Its unique design features a sliding headstock and guide bushing system that provides exceptional support to the workpiece during machining operations. This configuration allows for:
– Reduced vibration and deflection
– Improved dimensional accuracy
– Capability to machine long, slender parts
– Simultaneous multi-axis machining operations
The guide bushing acts as a support point very close to the cutting tool, minimizing workpiece movement and enabling precise machining of delicate parts that would otherwise be challenging to produce.
## Key Advantages of Swiss Screw Machining
### 1. Exceptional Precision
Swiss screw machines can achieve tolerances as tight as ±0.0002 inches (0.005mm), making them ideal for medical devices, aerospace components, and electronics parts.
### 2. High Production Efficiency
These machines often incorporate multiple tool stations and live tooling capabilities, allowing for complete part machining in a single setup. This significantly reduces cycle times and increases throughput.
### 3. Versatility in Materials
Swiss screw machining can handle a wide range of materials including:
– Stainless steels
– Titanium alloys
– Brass and copper
– Plastics
– Exotic metals
### 4. Cost-Effectiveness for Small Parts
For high-volume production of small, complex components, Swiss machining often proves more economical than conventional CNC turning due to reduced material waste and faster cycle times.
## Applications Across Industries
Swiss screw machining serves numerous industries with its precision capabilities:
### Medical Industry
– Surgical instruments
– Implant components
– Dental parts
– Micro-sized medical devices
### Aerospace and Defense
– Fuel system components
– Hydraulic fittings
– Sensor housings
– Fasteners and connectors
### Electronics
– Connector pins
– Shafts for miniature motors
– Precision spacers
– RF components
## Choosing the Right Swiss Screw Machining Partner
When selecting a Swiss machining provider, consider these factors:
– Experience with similar parts and materials
– Quality certifications (ISO, AS9100, etc.)
– Equipment capabilities and technology level
– Quality control processes
– Prototyping and production capacity
The best partners will offer design for manufacturability (DFM) feedback to optimize your parts for Swiss machining processes.
## Future of Swiss Screw Machining
As manufacturing demands continue to push for smaller, more complex components with tighter tolerances, Swiss screw machining technology continues to evolve. Modern advancements include:
Keyword: Swiss Screw Machining
– Integration with Industry 4.0 technologies
– Improved automation for lights-out manufacturing
– Enhanced multi-tasking capabilities
– Smarter tool monitoring systems
– More sophisticated CNC controls
These developments ensure Swiss screw machining remains at the forefront of precision manufacturing for years to come.
## Conclusion
Swiss screw machining represents the gold standard for producing small, precision components with complex geometries. Its unique capabilities in handling delicate workpieces while maintaining exceptional accuracy make it indispensable for industries where precision is non-negotiable. As technology advances, Swiss machining continues to push the boundaries of what’s possible in micro-manufacturing, offering manufacturers reliable solutions for their most challenging part requirements.